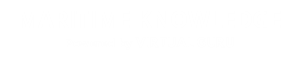
BASIC METALLURGY
Cast Iron
Cast Iron is an iron-carbon alloy with a typical carbon content of 3.0-4.5 wt.%. Also Si (0.5-3.5 wt.%) and small amounts of Mn are always present. The main advantages of cast iron are its low price and the ability to make products of a complex shape in a single production step. Furthermore, cast iron offers a reasonable resistance against corrosion. In general, the mechanical properties are lower than those of cast or wrought steels, especially when loaded in tension. In compression high loads can be supported. The mechanical properties of cast iron depend on the morphology of the carbon. This morphology depends on composition and process parameters.
Iron Carbon Diagram
Cast Steel
Iron alloy with carbon up to 1.7 wt.%. Mechanical properties are generally lower than wrought steels of the same composition, but in return, more complicated products can be made in one step. Mechanical properties of cast steel are better than cast iron but the casting properties are worse. High carbon cast steels offer excellent wear resistance.
Alloy Steel
Alloy steels differ from carbon steels in that they contain a high proportion of other alloying elements and they have better strength, ductility and toughness.. The following are regarded as the minimum levels. Alloy steels are classified according to increasing proportion of alloying elements and also phase change during heating and cooling as follows:
Gun Metal
Gun metal contains 10 percent tin, 88 percent copper, and 2 percent zinc. The zinc is added to clean the metal and increase its fluidity. It is not suitable for being worked in the cold state but may be forged when at about 600ºC. The metal is very strong and resistant to corrosion by water and atmosphere. Originally, it was made for casting boiler fittings, bushes, bearings, glands, etc.
Aluminium
Pure aluminium is available in grades from 99% to 99.99% purity. It is soft and ductile but work hardens. Pure aluminium is difficult to cast. It has a property of low density, good electrical conductivity, and high tensile, high corrosion resistance.
CHOICE OF MATERIAL FOR VARIOUS ENGINE PARTS
LAB TESTS
1. TENSILE TEST
AIM
To determine the tensile properties of the given specimen and to study the piece and character of fracture using a Universal Testing Machine (UTM).
EQUIPMENTS
TERMINOLOGY
GAUGE LENGTH (Lo)
It is the prescribed part of the cylindrical or prismatic portion of test piece on which elongation us measured at any movement during the test.
PERCENTAGE ELONGATION AFTER FRACTURE
It is the variation of the gauge length of test piece subjected to the fracture expressed as a percentage of original gauge length (Lo)
§o= the original cross-sectional area of specimen
ULTIMATE LOAD
It is the maximum load which the piece stands during test.
NORMAL BREAKING STRESS
It is the breaking load divided by original area of the section
ACTUAL BREAKING STRESS
It is the breaking load divided by actual area of the section.
TENSILE STRENGTH (Rm)
It is the ultimate load divided by original cross-sectional area of test piece.
YIELD STRESS
In steel which exhibits a yield phenomenon plastic deformation continues to occur at nearly constant stress.
PERMANENT SET STRESS
The stress at which after removal of a load a permanent elongation expressed as a % of original gauge length results.
PRINCIPLE
Up to limit of proportionality A, the material obeys hooks law and so the curve will be a straight line. point B is the limit of elasticity up to which bar can be loaded without any permanent set i.e. on removing load, the whole deformation will vanish beyond point B the rate of increase in stain will be more till the point C is reached where the materials undergoes additional strain without increase in stress and then undergoes plastic deformation this is known as yield point and stress known as yield stress actually at this point there is a drop in stress and yielding commences
After yielding only any further increase in stress will cause considerable increase in strain and curve raised till the point D is reached which is known as point of ultimate stress, the deformation in this range is party elastic on continuing the loading as the curve reaches ,E the bar breaks.
Modulus of elasticity E= PL / A with usual rotations, from the straight line graph between load and extension P/A can be determined measure L, A, and calculate E
During loading at a particular point load remain constant for few seconds and again goes on increasing. Point corresponds to yield point, stress at that point gives yield stress.
Percentage elongation = Final length – Original length / Original length × 100
Percentage reduction of area=Original area – Final area / Original area × 100
PROCEDURE
RESULT
(1) Yield stress =
(2) Normal breaking stress =
(3) Actual breaking stress =
(4) % Elongation on gauge length =
(5) % Reduction in area =
(6) Young’s modulus =
2. IMPACT TEST
The classical definition of Impact strength is the energy required to fracture a given volume of material. The impact test involves a pendulum or striking hammer swinging down from a specified height ‘h’ is used to hit the test piece. The specimen is held vertically as a cantilever between two jaws in such a way that the striking hammer strikes the specimen on the same face as that of notch. The notch is usually a V-notch which is ensure that the specimen will break as a result of the impact load to which is subjected. The height ‘h1’ to which the pendulum rises after striking the piece is a measure of energy used in breaking the pieces. The greater the energy used in breaking the lower the height to which the pendulum rises. Thus the energy used to break the piece is wh-wh1 where ‘w’ is the weight of the pendulum. The fracture of material can be either brittle or ductile.
There are two types of impact tests
(a) CHARPY TEST
The Charpy test is carried out on a piece (specimen) has a 2mm deep notch at its center making an angle of 45˚. The specimen is placed horizontally as simply supported beam between two anvils 40mm apart in such a way that the striking hammer strikes the piece on the face which is opposite to the notch.
(b) IZOD TEST
The Izod test is carried out on a piece (specimen) has a 2mm deep notch at its center making an angle of 45˚. The specimen is held vertically as a cantilever between two jaws in such a way that the sticking hammer strikes the specimen on the same face as that of notch.
IMPACT TEST
AIM
To determine the impact strength of the given standard specimen using Charpy/Izod impact test.
MATERIALS REQUIRED
GENERAL
Impact strength is used to measure a materials ability to withstand shock loading, It has been observed that a metal may be hard, strong or of high tensile strength. But it may be unsuitable for uses where it is subjected to sharp blows.
The capacity of a metal to with stand such blows (shock loading) without fracture is known as impact resistance.
The classical definition of impact strength is the energy required to fracture a given volume of material. The impact tests can be used as an indicator of toughness. The greater the value given by the testes the tougher the material. This testis (Charpy or Izod) can also be used to determine whether heat treatment of metal has been successfully carried out or not.
PROCEDURE
3. TYPES OF FRACTURE
Fracture is the separation of a body under stress into two or more parts. This is usually characterized as either brittle or ductile.
BRITTLE FRACTURE occurs by very rapid propagation of a crack after little or no plastic deformation. In crystalline materials brittle fracture usually precedes as granular appearance because of changes in orientation of these cleavage planes from grain to grain.
DUCTILE FRACTURE is fracture occurring after extensive plastic deformation and is characterized by slow crack propagation and surface has a characteristic dull, fibrous appearance.
4. HARDNESS TEST OF MATERIALS
The hardness represents the ability of a material to resist scratching, abrasion, cutting or penetration. The hardness test of a test material is generally performed to know its resistance against abrasion, penetration.
The testes commonly used are