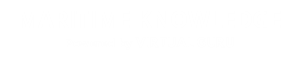
General considerations for design of boilers
Specific Learning Objectives:
After going through the topic student should be able to,
Introduction
Steam is a form of water and thus available in plentiful in the world. On board a ship, surrounded by the sea, it is possible to evaporate the salt water and produce distilled water which has very low solid content. It is this water which is fed into the ship's boilers to produce steam. The heat energy comes from burning the oil in the boiler furnace. The enclosed boiler is where the steam is collected at high pressures on top of the water inside the drum. The steam, thus produced , goes for further transformation by absorbing more heat from flue gas outside the drum to become superheated vapor which is fed to the turbines to produce work. As water is heated, boiled to steam vapors and further superheated, the steam carries progressively more heat energy as its pressures and temperatures are raised in the boiler system.
So, the real job of the water or the steam is just carrying the heat from combustion of fuel in the gas side of the boiler, and deliver that to the heat engines. Whatever heat is not able to be absorbed by the turbine engine (heat engine) is rejected with the exhausted steam to the Condenser; the exhaust steam is condensed and recycled back as feedwater to the boiler. During the passage, water or steam acts only as a carrier of heat and does not gets spent or consumed; except for some small leakage through pipelines and atmosphere due to evaporation and radiation. If you ignore those losses, the entire steam (in the form of recycled water) goes back to the boiler. And, the steam and water goes round and round the plant in a cyclic process. This is called a steam cycle.
The steam is such a fluid, which when pressurized, carries increasingly more heat and it's temperature can also be raised to make it into a superheated steam outside the boiler drum, so that it can carry even more heat and then deliver that to the turbines in the form of a high temperature and pressure steam which gets expanded through the turbine stages - thereby consuming the heat brought in by the steam and convert the pressure drops and changes in velocity into work by rotating the turbine wheels, which ultimately moves the ship's propeller.
Definition and Terms
There are a number of technical terms used in connection with steam generation. Some of these commonly used terms you should know are as follows:
Fire Tube Boiler
As it indicated from the name, the firetube boiler consists of numbers of tubes through which hot gasses are passed. These hot gas tubes are immersed into water, in a closed vessel. Actually, in fire tube boiler one closed vessel or shell contains water, through which hot tubes are passed. These fire tubes or hot gas tubes heated up the water and convert the water into steam and the steam remains in same vessel. As the water and steam both are in same vessel a firetube cannot produce steam at very high pressure.
Water Tube Boiler
Watertube boiler is reverse of the fire tube boiler. In water tube boiler the water is heated inside tubes and hot gasses surround these tubes.
A water tube boiler is a type of boiler in which water circulates in tubes heated externally by the fire. Fuel is burned inside the furnace, creating hot gas which heats water in the steam-generating tubes. In smaller boilers, additional generating tubes are separate in the furnace, while larger utility boilers rely on the water-filled tubes that make up the walls of the furnace to generate syeam.
The heated water then rises into the steam drum. Here, saturated steam is drawn off the top of the drum. In some services, the steam will reenter the furnace through a superheater to become superheated. Superheated steam is defined as steam that is heated above the boiling point at a given pressure. Superheated steam is a dry gas and therefore used to drive turbines, since water droplets can severely damage turbine blades.
Cool water at the bottom of the steam drum returns to the feedwater drum via large-bore 'downcomer tubes', where it pre-heats the feedwater supply. (In large utility boilers, the feedwater is supplied to the steam drum and the downcomers supply water to the bottom of the waterwalls).
The water tube boiler is used to generate steam having high pressure and temperature. These small internal parts produce high volume steam for high-capacity applications.
Water tube boilers are the most widely used boilers. These type has replaced many boilers, including the fire tube type, mainly because of the following reasons:
Uses of steam on ships
Copyright VIRTUAL GURU © 2025. All Rights Reserved.