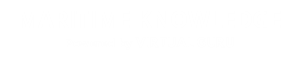
Pneumatic technology deals with the study of behavior and applications of compressed air in our daily life in general and manufacturing automation in particular. Pneumatic systems use air as the medium which is abundantly available and can be exhausted into the atmosphere after completion of the assigned task.
1. Basic Components of Pneumatic System :
Components of a pneumatic system
Important components of a pneumatic system are shown in fig.
a) Air filters: These are used to filter out the contaminants from the air.
b) Compressor: Compressed air is generated by using air compressors. Air compressors are either diesel or electrically operated. Based on the requirement of compressed air, suitable capacity compressors may be used.
c) Air cooler: During compression operation, air temperature increases. Therefore coolers are used to reduce the temperature of the compressed air.
d) Dryer: The water vapor or moisture in the air is separated from the air by using a dryer.
e) Control Valves: Control valves are used to regulate, control and monitor for control of direction flow, pressure etc.
f) Air Actuator: Air cylinders and motors are used to obtain the required movements of mechanical elements of pneumatic system.
Many systems require a high volume at low pressure for rapid movement of a vise or tool, then low volume at high pressure for clamping or feeding. This can be accomplished by a high-low circuit using two pumps.
During rapid traverse, both pumps supply the system. When pressure rises during clamping or feed, the large-volume main pump unloads, and the small pump maintains pressure. Output flow of the small pump is low enough to prevent heating of the oil. Instead of pilot operation, the unloading valve can be solenoid controlled and actuated by a pressure switch.
ELECTRONIC CONTROL
Electronic control in mobile equipment can consist of the following:
Operator Inputs:
These inputs can be defined as the user interface, and can consist of joysticks, potentiometers, operator panels, or other input devices.
Feedback Inputs:
These inputs can be defined as the machine interface, and can consist of pressure transducers, temperature sensors, flow sensors, velocity sensors or RPM sensors. When feedback inputs are used the system is described as “closed loop.”
Controller or ECU:
This is the brains of the electronic control. It processes the inputs and converts them into a defined output to the hydraulic system. The controller also can have the ability to receive feedback inputs from machine sensors and attenuate its outputs accordingly. The controller can be factory-programmed or have the ability to be user-programmable to meet the specific needs of the application.
Outputs:
Outputs can be on/off voltage signals or proportional PWM signals to control the hydraulic valving.
Communications:
The controller can have the ability to engage in two-way communications with a bus system (for example: communication between the ECU and a display, or output signal to an input device).
ECUs were developed to replace the older “sequential relay circuits,” that were used for machine control. The ECU works by measuring its inputs and depending on their state, switching its outputs On or Off. The user enters setup instructions, usually via software, that will produce the desired results. Because many of the controller’s functions are user-programmable, an ECU has the versatility to be field-modified for changing applications or conditions.
Some ECUs have the capability to convert analog inputs, process them digitally, and produce analog outputs. ECUs that do not have built-in converters require separate analog to digital converters to convert the input.
An analog signal is an AC or DC voltage or current, or resistive signal that varies smoothly and continuously. In an analog system, a physical variable is represented by a proportional voltage that varies in correspondence with the physical variable. Electronic circuits that process analog signals are called linear circuits.
An example of an analog device is a traditional-style clock that has hour and minute sweep hands that rotate around the dial. As an input, an analog signal can provide infinite resolution due to its wide frequency range.
Digital signals vary in discrete (discontinuous) values to represent information for input. A digital signal is normally in the form of a series of pulses that rapidly change from one distinct, fixed voltage level to another.
An example of a digital device is a clock that displays the time in actual numerals that change in one-numeral increments. As an input, the resolution is dependent on the number of bits of information processed or available to the controller. In digital systems, physical variables are represented by numerical values using the binary (base 2) number system.
Some of the different forms that mobile electronics can take are described in the chart shown on this page. There is an increasing complexity and cost as the controllers move from single-function analog controls to complete complex digital control systems.
Digital vehicle controllers offer a high level of sophistication by executing a programmed sequence of functions that constantly control all motion parameters.